D SERIES
Makino D-Series Vertical Machining Centers for Machining Aerospace Components
Designed for small-to-medium-size aerospace components, Makino’s D-Series 5-axis vertical machining centers enable manufacturers to reduce setups, slash cycle times and achieve precision accuracies in complex titanium machining processes. Their ultra-high-torque, direct-drive rotary table design provides outstanding positioning accuracy and repeatability with superior acceleration and rotational speed for cycle time reduction of up to 60 percent in complex, three dimensional titanium machining applications. For enhanced productivity, all D-Series machines can be easily upgraded for automation with an automatic pallet changer.
D300
Workzone: 11.8"(X), 19.7"(Y), 13.8"(Z)
Type: Vertical Machining Centers 5 Axis
Learn More
D500
Workzone: 21.6"(X), 39.4"(Y), 19.7"(Z)
Type: Vertical Machining Centers 5 Axis
Learn More
Related Content
-
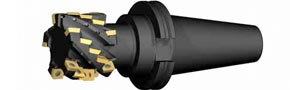
Highly Efficient Machining for Titanium Aerospace Structures
//20 min
Click to View
Highly Efficient Machining for Titanium Aerospace Structures
//20 min
Executive Summary
Tool selection in the machining of titanium is unlike that of standard material processing. Based on the part geometries and specifications of the machining center, new considerations should be taken into account in choosing the most efficient tools for the job. In this presentation, Kennametal looks at how to define efficient processing of titanium through a variety of case studies. By evaluating specific challenges, solutions and other background details, the presenter determines how manufacturers can gain a competitive edge in their titanium machining processes with a complete tooling solution set.
-
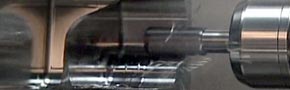
Efficient Machining Solutions in Titanium Alloys
//25 min
Click to View
Efficient Machining Solutions in Titanium Alloys
//25 min
Executive Summary
Highly efficient machining of titanium looks not just at the machine tool, but also machining conditions, such as tooling, tool paths, cutting speeds, depth of cut and temperatures in the cutting zone. In order to drive down costs, manufacturers must optimize all critical aspects of the cutting zone for greater productivity and extended tool life. This presentation discusses the collaboration of ATI’s metallurgists, scientists and engineers in providing an effective understanding, techniques and solutions for improving the machinability of titanium alloys. Through the data they collected, ATI examines all factors that impact the machinability of titanium, including machine tools, component material, machining conditions and the cutting-zone environment. Specific considerations are given to cutter geometries and how they influence conditions of metal removal and temperature.
-
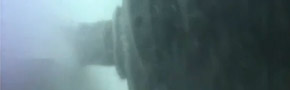
Deeper Cuts, Higher Metal Removal Rates and Reduced Tool Wea…
//13 min
Click to View
Deeper Cuts, Higher Metal Removal Rates and Reduced Tool Wear with ADVANTiGE Active Damping System
//13 min
Executive Summary
Deeper Cuts, Higher Metal Removal Rates and Reduced Tool Wear with ADVANTiGE Active Damping System
By adjusting frictional forces based on low frequency vibration sensing, the ADVANTiGE Active Damping System avoids chatter and cutter damage resulting from structural resonance in real time. This vibration suppression enables deeper cuts, higher metal removal rates and reduced tool wear.
This presentation describes in detail the principles of vibration damping and machine rigidity, including the four major components to Makino’s Active Damping System.
Additional examples in this presentation also show the significant differences between conventional cutting performances and those enhanced by Active Dampening.
Shinichi Inoue
Sitae Re Volupta Tquidus
//35min
Executive Summary
Evereprepudi dolorum eum excea et occus quias aut ea voluptatur antur assuscia nus, con re volupta tumqui que evenihita eostiatus experem quo ea destrum qui opta cum nessit abo. Neque volesto rionsequamus re solorpo ritium quatinc tecabo. Namet odior re simodigenis earchil inis ra con perumquis doluptassum nobis sim adissed eic tem estist ani doloressit aut adisinu lparibus dem as nulparumque prectio de cusaped itatend errorat laces accum rerum et asitae recus am, occuptaquos et ea impor rere, sintur, sin corecat.
Tionet landi repudae rferro ommos il earum vid et mil ius exped et mos et quo eosto blamet as esedit apelibu scitatur sum, explitia volupta tempor aut magnit, ommolendant, corum is elicipsunt que vel iliqui di audam eaquos num abo. Architem venihilicium di ommo odit eum in pe imi, optis et ped